**Spoiler alert** We do not just "slap on a coat of paint".
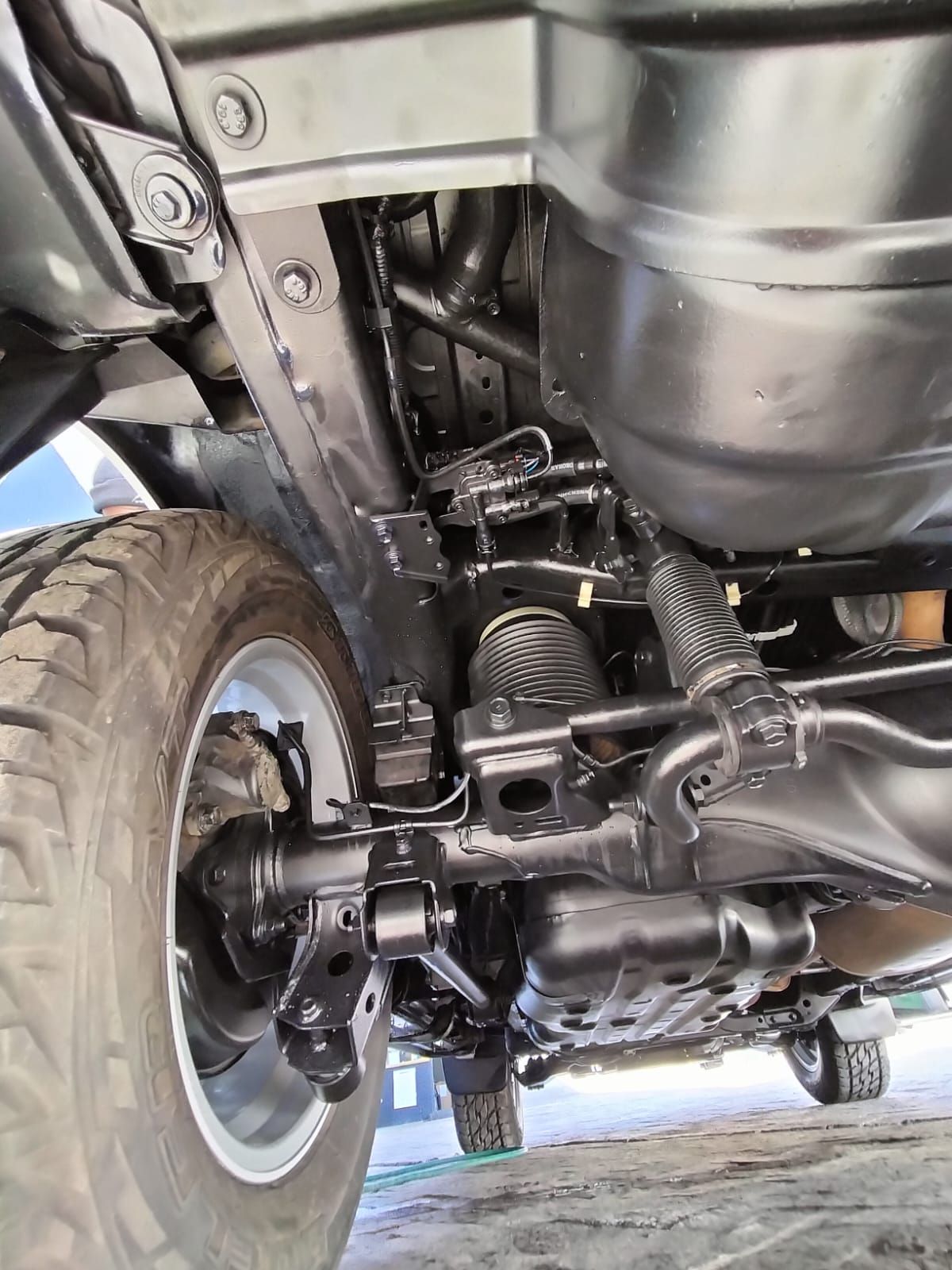
Lately, some manufacturers are excluding chassis corrosion damage from their warrantees, so looking into rust protection on the chassis and underbody has become the next step in vehicle maintenance.
When it comes to a long term, durable and effective anti-corrosion chassis treatment, Anthony has perfected the process.
After almost 30 years as a high-end detailer, with most spent researching more effective ways to treat and prevent chassis corrosion, the Anthony Military Treatment checks every box, from aesthetically pleasing to tough as nails with sky high corrosion preventive properties.
As one would imagine, restoring a vehicle chassis to near as factory finish as possible, is not an overnight project.
A minimum of five to six working days are required for an Anthony masterpiece.
Sud 'n scrub.
Proper Preparation Prevents Poor Performance. This is true in life and chassis.
The best coating in the world will not adhere to an incorrectly prepared substrate. Thorough cleaning is essential.
A heavy-duty degreaser is applied with a foam cannon, agitated with a brush and then rinsed off using high-pressure hot water and steam. This process is repeated until the chassis is completely devoid of all grease, road grime and all mud and sand stuck in various nooks and crannies.
We do ask that you please have the chassis cleaned of excess mud before booking in. Excessively dirty chassis are charged extra for cleaning.
Remember how Granny's kitchen sink used to shine? We would make her proud.
Out! Out! Damned rust!
Much like Lady McBeth's blood-stained hands, established rust is notoriously hard to remove. Converters have proven to be ineffective and a more hands-on approach is needed. We use chelating agents, which neutralise the rust, causing it to fall from the substrate, leaving clean metal behind. Sometimes the rust has eaten so deep into the metal that nylon brushes, flapper discs and good old elbow grease and sandpaper are the only ways to remove it. We try to stay clear of wire brushes as they have a tendency to break, leaving wire particles embedded in the chassis, which will cause rust to form in those areas.
Should we find that the chassis integrity has been compromised by the depth of the corrosion, we will inform the customer and have those sections repaired by cutting out the affected areas and welding in new sections.
Wrap it like a birthday present.
Now that the chassis is clean and rust free, the final preparation stage begins.
First, the entire body of the vehicle is wrapped with industrial pallet wrap. We take special precautions to avoid overspray on the body of the vehicle.
All plastic and rubber components, shocks, brake calipers, exhaust and gearbox (including the transfer case) are covered up with masking tape and wrapping material. Our aim is to restore that chassis to as close to factory quality as possible.
Our team even tape up serial number plates and stickers, to ensure complete restoration to its original glory!
New coat. Wear it like a Boss!
Finally, we are ready for the first coating.
Our Heavy Duty Marine Coating is applied first. This coating is manufactured for us, is not freely available on the market, and comes with a Milspec certification. Flexibility and durability, with top shelf anti-corrosion properties and incredible adhesion, makes this coating, in our opinion, the Rolls Royce of chassis coatings. This coating is guaranteed to not flake, peel, crack or rust creep. Should the paint break due to mechanical removal, touch ups are quick, as only the affected area needs to be treated, unlike other coatings where the entire coating needs to be removed first and then recoated.
The entire chassis, underbody, wheel wells and hubs are treated. Every. Single. Nook. And. Cranny.
Being a thin film coating, nuts and bolt sizes are not affected. Your mechanic will be grateful.
Important to remember. Even though the paint is touch dry upon collection, 10 days curing is required before taking the vehicle on an off-roading adventure.
Pass the lube, babe.
The paint coating has dried, the chassis looks spectacular.
Now for the final coating, also acting as an additional sealant.
Our Corrosion Preventive, Penetrating Drying Oil is exactly what it claims to be.
Goes on like an oil, penetrates the substrate and dries up, leaving a barrier that has been salt, acid and alkaline drag tested. Cleaning after a bit of fun in the mud now becomes much easier as dirt should fall off readily when rinsed with water.
This oil is also applied behind the fenders and any other hard to reach areas where a paint coating is not advised.
The chassis cavity is treated with a Corrosion Preventive, Drying Wax. This wax is also used between overlapping plates and between the leaf springs, in as much as we can reach these areas with our equipment.
What?! There is more?!
Of course, there is...
Being an Auto Cosmetician at heart, Anthony strives to present every vehicle in a condition that would make a dealer principal giddy with pride.
The water channels below the door panels are cleaned and the cavity is coated with the same drying oil as used on the chassis. All nuts, bolts and hinges around the door panels are also treated with this clear coat.
The engine bay is detailed by hand, and nuts, bolts and hinges are treated with the drying oil. The bonnet cavity is also coated.
Before collection, the vehicle is rinsed, dried and prepped for delivery.
If you opt for the Military Plus Option, you can also expect a full body decontamination (industrial fallout removal), stage 1 polish, UV Protective coating and a mini-interior.
Just take my money, please!
With proper care and maintenance, an Anthony Chassis will last for years.
No coating is bullet proof, and we understand that most vehicles sporting our treatment will spend extensive time in the bush, on the beach and in the dunes. When chips and sandblasting happen, do not fret. Touch ups are on the house, if you bring your vehicle in for a paid chassis clean every 6 to 12 months, depending on the punishment the chassis endured.
Mechanical removal, or rust forming underneath the original factory coating/rubberising is excluded. Removal of the factory coating/rubberising prior to coating is possible and quoted additionally.
All in all, money well spent, adding years to the longevity of your vehicle, and giving you the peace of mind that the spine of your vehicle will not deteriorate due to corrosion.
Anthony Anti-Corrosion Coatings and Supplies BLOG
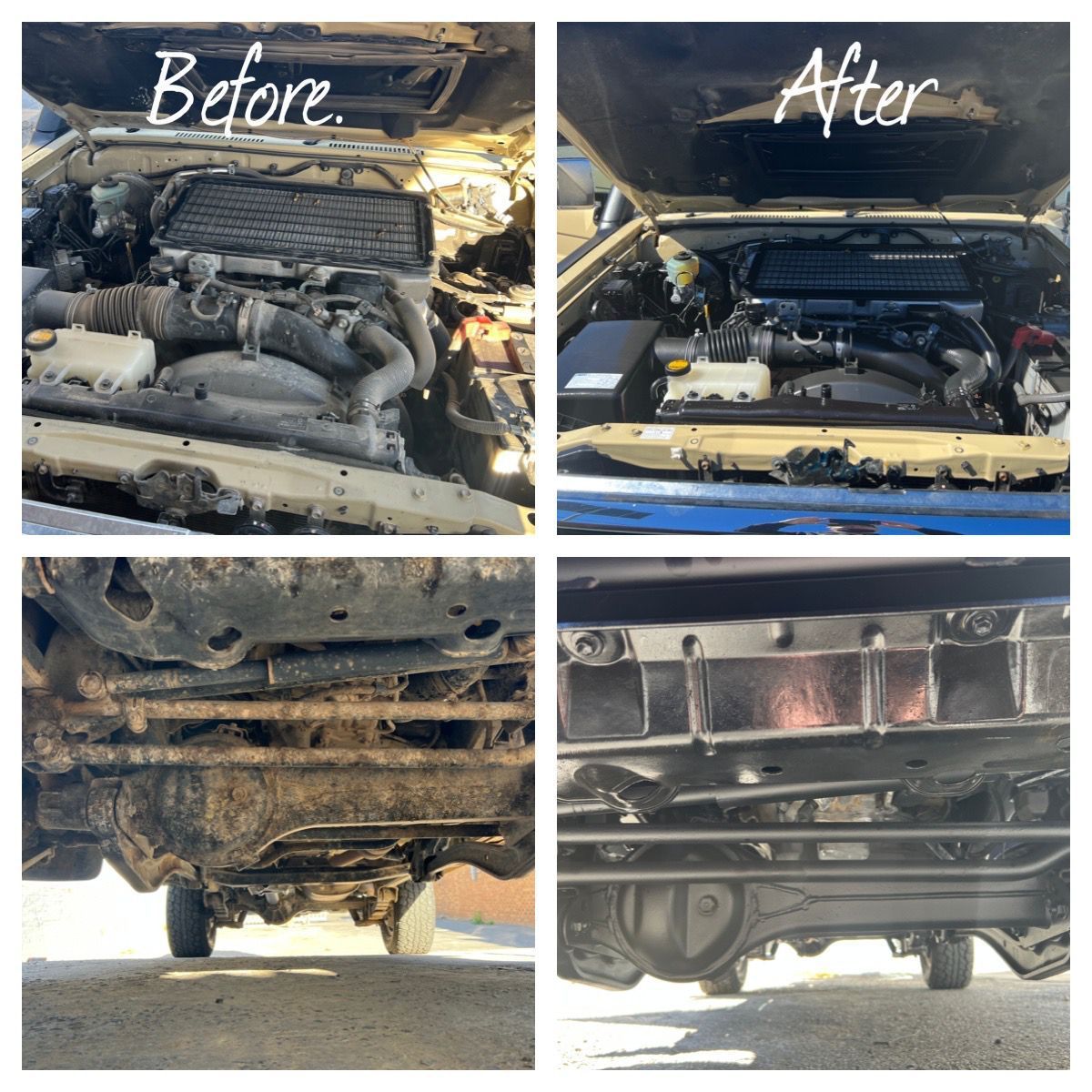
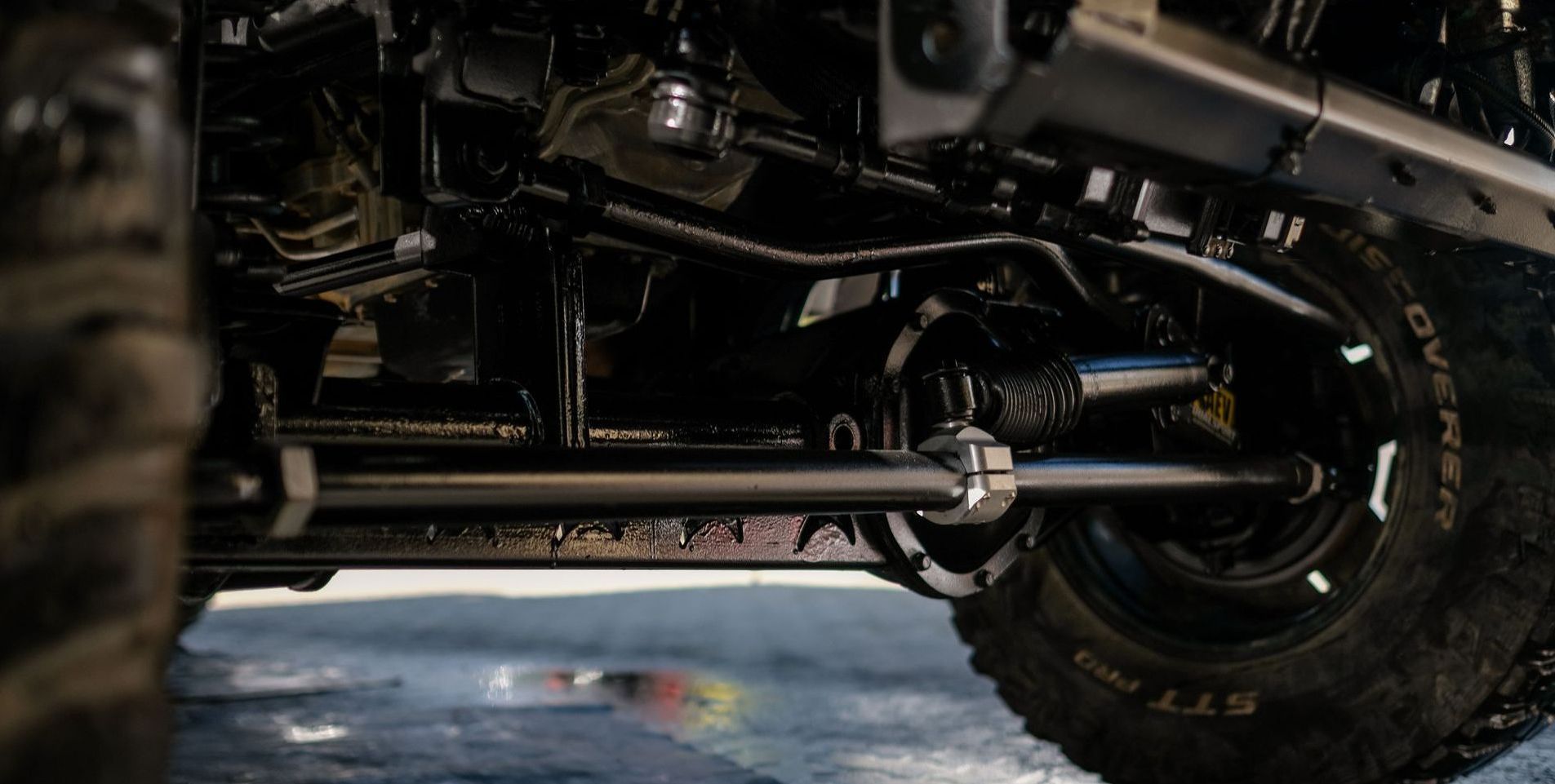